Pipes SAW
- Pipe Length 6-16 m (as standard and special lengths up to 24m)
- Outside Diameter 219.1 – 3048 mm.
- Wall Thickness 4 – 26 mm.
- Raw Material hot rolled steel coil
- Welding Process submerged arc welding
Production Standards
The both plants are planned mainly for the production of the pipes in API standard, also manufacture pipes in accordance with AWWA, DIN,BS, ASTM and Turkish Standards to serve to the petroleum, gas, waterline projects and construction industry. Noksel supplies spirally welded steel pipes in the following standards according to usage areas.
- Petroleum and Gas Line Pipes: API 5L, ISO 3183, TS 6047, DIN 17172, GOST 20295, EN 10208-2
- Water Line Pipes: EN 10217-1, DIN 1626, AWWA C200, DIN 2460, BS 534, UNI 6363, EN 10224
- General Purpose Pipes: BS 3601, DIN 1626
- Piling Pipes: ASTM A 252
- Pipe Joints and Specials: AWWA C208, BS 534
Quality Control / Assurance
Noksel, has a quality control system including all production processes starting from raw material and continuing with welding wire and flux till to transportation. This system is managed by a computer based program called SAP, which prevents human error in a great extend.
Noksel, by establishing a detailed Quality ISO 9001:2000, Enviromental ISO 14001:2004, Health and Safety OHSAS 18001:1999 management systems aiming to be a leader in its own market competition as a major principle.
Quality Control is Noksel’s one of the most important function that all the required tests and inspections are carried out in compliance with the customer requirements and related standards by using modern inspection and testing equipments.
- Automatic Ultrasonic Inspection
- Hydrostatic Test
- Radioscopic Inspection
- Off-Line Ultrasonic Inspection
- Manual Ultrasonic Inspection
- Magnetic Particle Inspection
- Liquid Penetrant Inspection
- X-Ray Film Radiographic Inspection
- Dimensional Inspection
- Mechanical Laboratory Tests
- Tensile Test
- Guided Bend Test
- Charpy Impact Test
- Hardness Test
- Chemical Analysis
- Metallographic Inspection
- Drop Weight Tear Test
- Coating Laboratory Tests
- Glass Transition Temperature Test (DSC- Differential Scanning Calorimeter)
- Melt Flow Index Meter
- Cathodic Disbonding Test
- Indentation Hardness Test
- Polyethylene / Polypropylene Adhesion Test
- Polyethylene / Polypropylene Elongation Test
- Transverse Electric Resistivity Test
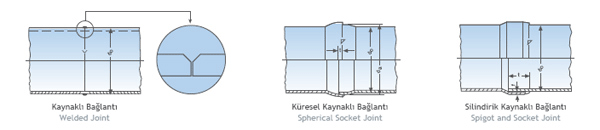
Pipe Joint Details
The following joint details can be selected by considering the utilization purpose and the dimension.
- Welded Joint:: he most widely used type for the joining of steel pipes. Steel pipe is relieved with bevelled ends which are made with special equipment in compliance with the relevant standards.
- Spherical Socket Joint: Provides the possibility of a rotation 10 degrees at the pipeline without the utilization of any special fittings. Steel pipes are welded from outside after proper erectioning according to required angle.
- Spherical Socket Joint with insulating sleeve: has same features of previous one adding saving of internal lining. Mainly used in Italian market.
- Spigot and Socket Joint: Especially used for the steel pipes inside coated with cement mortar. Steel pipes are welded from outside after erectioning.
- Flanged Joint: The special manufactured flanges are welded to the ends of the pipe and then jointed with bolts.
Lining and Coating
Air, water, soil and chemical substances and corrosive mediums effect the steel pipe as they effect everything. This effects can be eliminated by coating and lining of the pipe with suitable materials.
Noksel, believing the importance of the continuous high quality and good workmanship, offers 3 layer extruded Polyethylene, Epoxy, Bitumen, Coal-Tar Enamel and Cement Mortar coating and lining facilities to its customers.
Surface Preparation: Prior to the application of the coating, the surface of the steel pipes must be cleaned to make them free of impurities. For this purpose, internal and external surface of the pipes are shot-blasted to a standard degree of clean Sa 21/2 with a special care.
External Coating
- Epoxy Coating: AWWA C-210, NFA 49709, TS EN 10289
- Polyethylene Coating: DIN 30670, NFA 49710, TS 5139
- Polypropylene Coating: DIN 30678, NFA 49711
- Bitumen Coating: TS 4356, DIN 30673, BS 534
- Coal-tar Enamel Coating: AWWA C-203
Lining Coating
- Epoxy Lining: AWWA C-210, NFA 49709, TS EN 10289
- Bitumen Lining: DIN 30673, BS 534
- Cement Mortar Lining: AWWA C-205, BS 534
Transportation
Steel pipes after being manufactured completely are loaded with special apparatus used for the protection of the pipes and coatings during the loading operation. Transportation of pipes by vessels according to the API 5LW Recommended Practice for Marine Transport by Barges and vessels, handling and storage procedures are also based on API related customer requirements. Noksel’s factories are mainly available for the land, sea and railway transportation due to their proper locations.
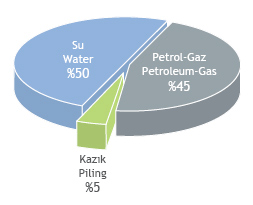
Utilization Areas of Steel Pipes:
The improved techniques and materials of today for the protection againts corrosion had also supplementary assistance to steel pipes for having longer lifes. Therefore, together with the other superior properties mentioned below, steel pipes have the advantages for usage purposes listed below among all other types of pipes.
Distribution of Manufactured Pipes According to Utilization Areas
Advantages:
- High Strength
- High Impact and Pressure Resistance
- High Carrying Capacity
- Stability and Long Life
- Elasticity
- Ductility
- Formability
Usage:
- Petroleum Pipelines
- Gas Distributing Pipelines
- Water Distributing Pipelines
- Piling Purposes
- Piles Industrial Pipelines
- Steel Structures
- Pressure Air Pipelines
- Refineries
- Transportation of Liquid Hydrocarbons
- Transportation of High Temperature Water
- Storage Application of Hydrocarbons